连续碳纤维热塑性复合材料的加工技术总结
热塑性碳纤维复合材料的制备难度较高,不仅要选择能够提高纤维与基体界面强度的上浆剂,而且还要选择合理的制备工艺。目前业内主流的工艺有熔融浸渍法、泥浆法等。无论是哪一种工艺,其中牵扯到的设备、技术和经验要求较热固性碳纤维都更具难度一些。

但考虑到热塑性碳纤维复合材料具备的各种性能优势,只要科技水平勉强可以达到制备标准,相信再困难再繁复,也会有众多的学者和机构争相尝试,一旦突破,就可能成为材料界的一个传奇。
热塑性碳纤维复合材料中,以连续碳纤维增强热塑性高分子复合材料的性能最优,连续形态的碳纤维更好的继承了碳纤维的各项机械性能,因此业内多种实验和尝试,大部分集中于此。
连续碳纤维热塑性复合材料可加工成外形各异但强度极高的工业零部件,可以为航空航天、轨道交通、尖端医疗等领域的科技探索提供强大的助力。想要将连续碳纤维热塑性复合材料加工成需要的产品,需要深刻了解该型复合材料的性能优劣,以此归纳出可行的加工方式。
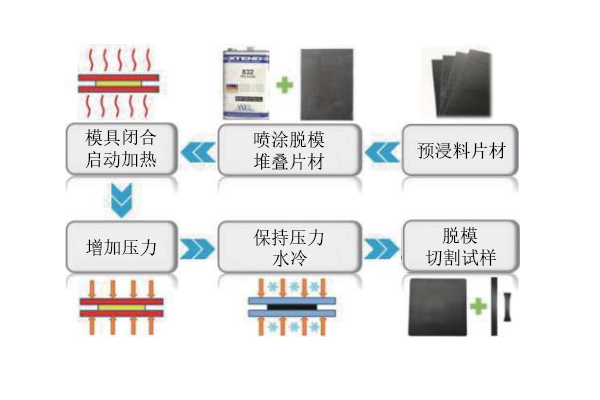
连续碳纤维热塑性复合材料可进行热压成型加工
由于热塑性高分子的熔融与凝固过程仅涉及物理变化,无需经过化学反应固化,这使热塑性复合材料不仅可以采用热固性复合材料的加工方式,同时也具备快速加工的可能。除了基础的热压成型外,热塑性碳纤维复合材料还可以使用冲压成型的加工方式。
1、热压成型:热塑性复合材料的热压成型是将预浸料在模具中铺覆后,经加温加压成型的技术,热压成型操作简单、质量稳定,是最为普遍适用的热塑性复合材料快速成型技术。目前已经发展成为一项成熟的热塑性复合材料零件制造加工技术,并已经在多种型号的民用机上成熟应用。
2、冲压成型:冲压成型是连续纤维增强高性能热塑性复合材料加工成型的一种常见方法。冲压成型工艺的成型周期短(数分钟计),生产效率高,另外冲压成型工艺可以制造出高强、高韧性的热塑性碳纤维零部件。
冲压成型过程简述:首先对连续纤维复合材料预浸料进行裁剪铺层,之后放置于烘箱中加热到高于基体熔融/软化温度约20~40℃。然后,将已加热的多层预浸料预成型体迅速转移到配有特定模具的闭合速度可控的压机中。当压机闭合时,预浸料变形贴合模具,其中熔融的基体在模具内压力作用下流动并填满模腔。之后,在整个冷却固结过程中保持一定压力,当模具的温度冷却到基体的熔融/软化温度以下时,基体会迅速冷却固化。
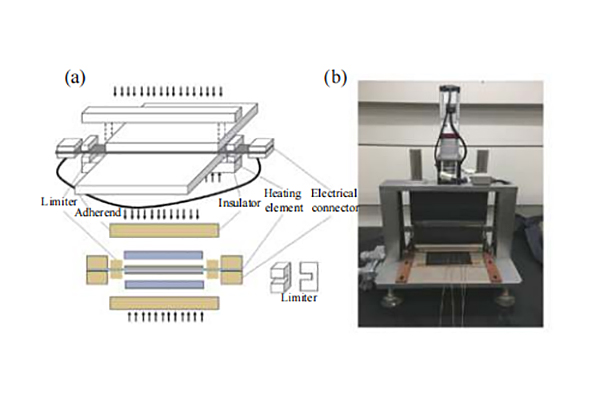
连续碳纤维热塑性复合材料可进行焊接加工
热塑性碳纤维复合材料的热重塑特性,使其具备了一项特殊的加工方法——焊接。焊接加工,又称为熔融连接,是通过将热塑性树脂作为焊料,经熔融后冷却将复合材料特定表面进行粘合的装配工艺。
热固性碳纤维复合材料制成的工业零部件,采用的连接方式为胶接、机械连接和预埋,而热塑性碳纤维复合材料有了新的选择。与传统的胶接和机械连接相比,焊接技术与基体匹配性更好,焊接加工的速度更快,效果更好。
根据产热机制不同,目前可以将焊接技术分为超声焊、感应焊、电阻焊及微波焊等。其中,电阻焊对设备要求较低,技术成熟度最高,能量获取方式简单,工艺控制简便可靠,材料体系适用性强,适用于大尺寸结构件的焊接,因此得到了广泛的应用。
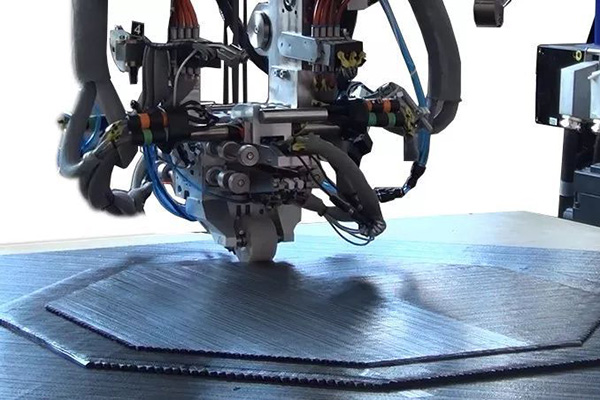
连续碳纤维热塑性复合材料可进行自动铺放加工
热塑性碳纤维复合材料未来的一大应用方向就是飞机制造,飞机机翼、襟翼、尾翼,还有表面的蒙皮都可以以此材料混合其他材料来制作,这就牵扯到一个重要的问题,那就是如何提高加工效率?
不管是热固性还是热塑性碳纤维,它们都存在一个弊端,那就是批量加工难度较高,产能无法大幅提升。针对此问题,科研和技术人员提出了对应的解决方案,即利用自动铺放技术进行自动化加工处理,利用机器和程序代替手工作业,解放产能,实现加工效率的飞速提升。
自动铺放技术原理是铺放头按一定的运动规律,以一定的角度输送预浸丝/预浸带,并通过恒定速率的压辊压在模具表面,实现复合材料铺叠自动成型。在铺放过程中,首先使用加热装置加热预浸丝/预浸带,然后用压辊对预浸丝/预浸带施加压力,预浸丝/预浸带在高温高压环境下实现原位固结。采用自动铺放技术,可显著降低生产成本和缩短加工时间。自动铺放不受加工场地和零件大小的限制,且复合材料构件在铺放过程中一次成型,适合于大尺寸曲面构件的铺贴和成型。
自动铺放加工可以完成重复性较高的工作,同时根据程序的升级,可以完成复杂性更高的工作,但是在实际运行中还是会存在很多bug,需要修复和反复验证。铺放速度、铺放压力、铺放温度等多项参数需要经过大量的调控,才能将自动铺放加工的效果达到期望的水平。
文章转载说明:本文由东台智上原创编辑发布,版权所有,未经允许不得转载。